In today's highly competitive manufacturing environment, continuously seeking ways to improve production efficiency and quality is crucial for the survival and development of enterprises. Lean tubes have emerged as a highly effective tool for enhancing production processes. Here are the reasons why we should use lean tubes to improve production.
First and foremost, flexibility is one of the most significant advantages of lean tubes. In the ever-changing manufacturing landscape, the ability to quickly adapt production lines to meet different product requirements is essential. Lean tubes can be easily assembled and disassembled, allowing for rapid reconfiguration of workstations, production lines, and storage areas. This flexibility enables companies to respond promptly to market changes, new product introductions, and fluctuating demand, reducing downtime and increasing productivity.
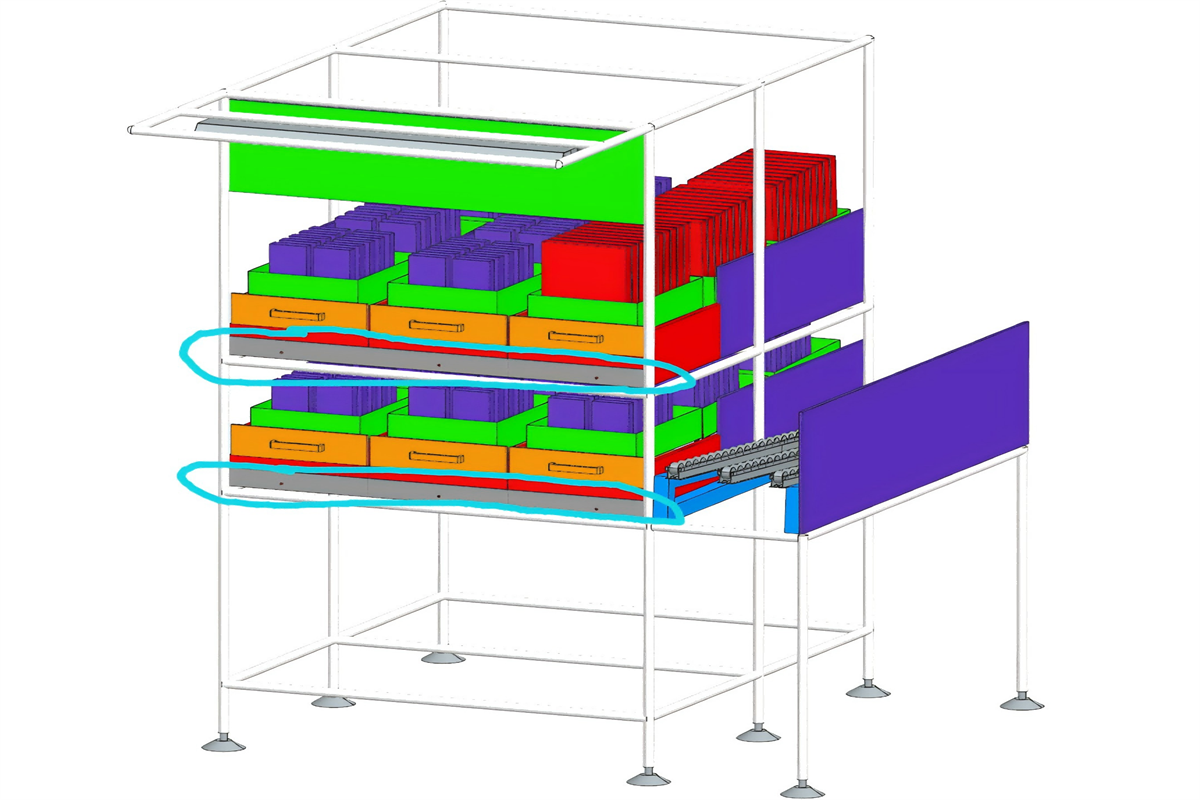
Moreover, lean tubes contribute to optimizing space utilization. Factories and warehouses often face space constraints, and efficient use of available space is vital for cost reduction and operational efficiency. Lean tube structures such as racks, shelves, and workbenches can be customized to fit specific spaces, making the most of vertical and horizontal areas. This not only helps in organizing materials and tools but also reduces clutter and improves workflow.
Another important aspect is improved organization and workflow. By using lean tubes to create dedicated workstations, storage areas, and material handling systems, companies can establish a more organized and efficient production environment. Materials and tools can be easily accessed when needed, reducing search time and minimizing waste. The clear layout and labeling of lean tube structures also facilitate communication and cooperation among workers, enhancing overall productivity.
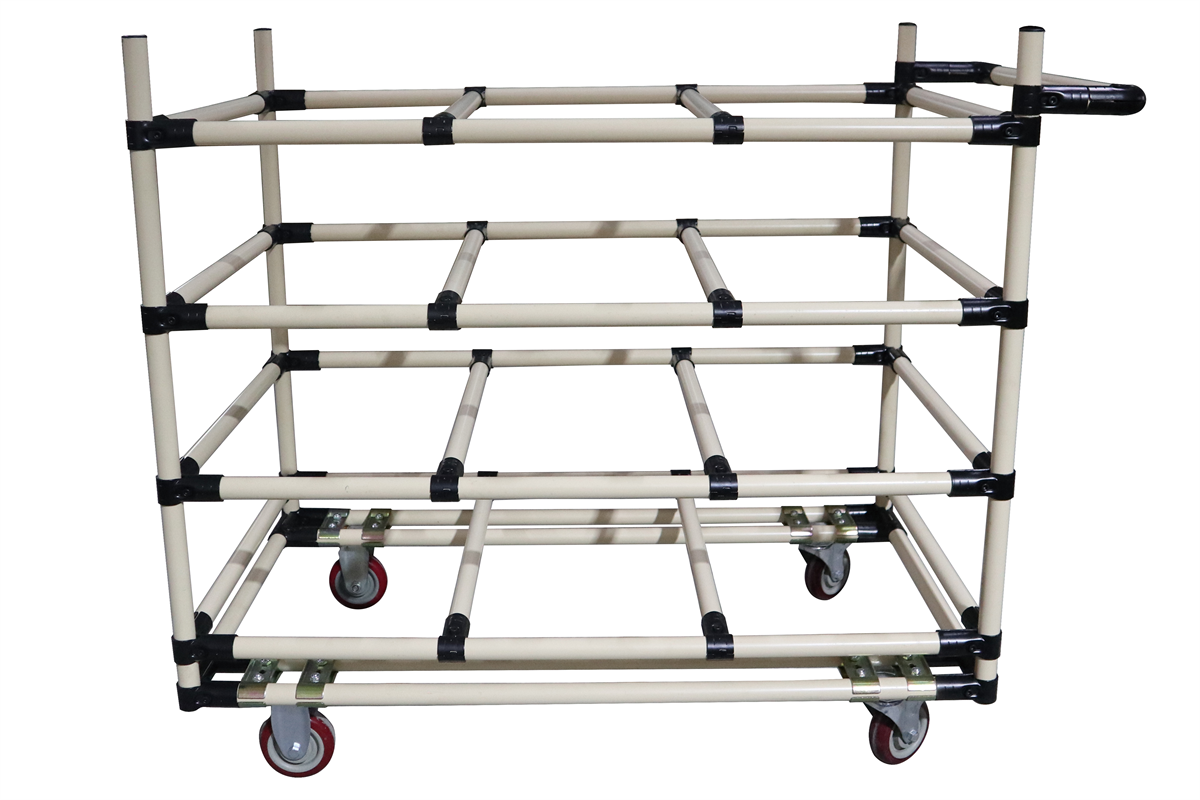
Lean tubes also support the concept of continuous improvement. As production processes evolve, it is essential to be able to make adjustments and improvements continuously. With lean tubes, it is easy to experiment with different layouts and configurations to find the most efficient setup. Workers can actively participate in the improvement process by suggesting changes and implementing them using lean tubes, promoting a culture of innovation and continuous learning.
Furthermore, lean tubes are cost-effective. Compared to traditional fixed infrastructure, lean tubes are relatively inexpensive and can be easily modified or expanded as needed. This reduces the investment cost for production line upgrades and expansions, making it more accessible for small and medium-sized enterprises.
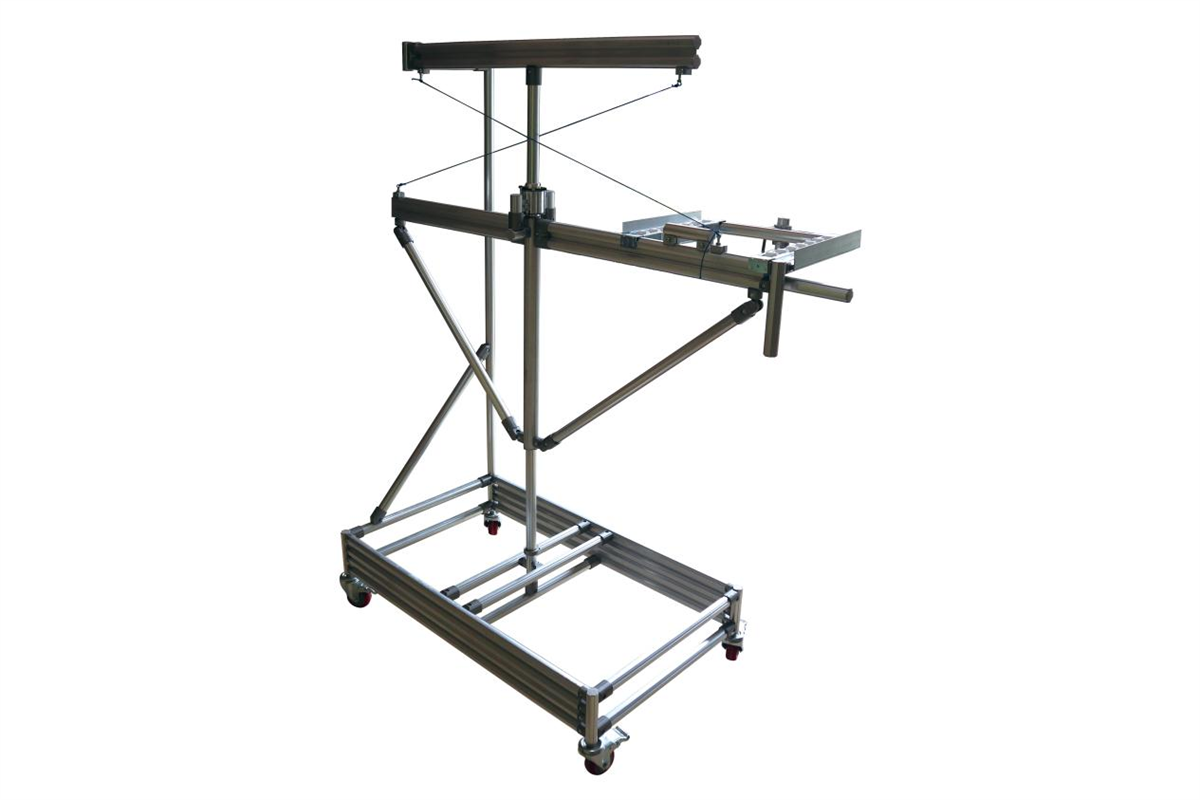
Our main service:
Welcome to quote for your projects:
Contact: zoe.tan@wj-lean.com
Whatsapp/phone/Wechat : +86 18813530412
Post time: Oct-22-2024